Bearing Lubrication
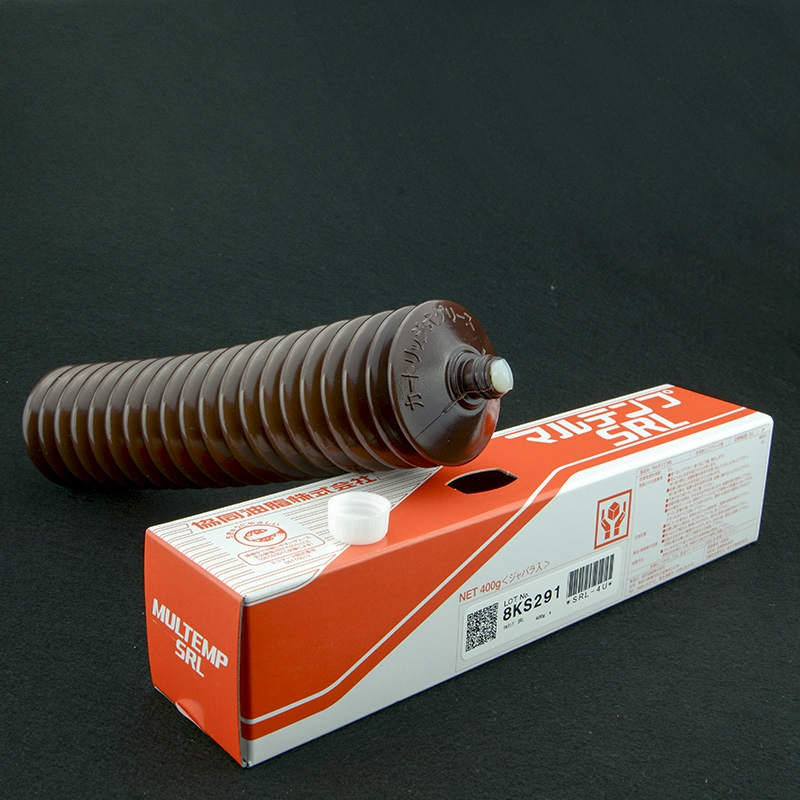
Bearing Lubrication Introduction:
Bearing lubrication is absolutely essential to the proper operation of all kinds of ball and roller bearings.
A proper lubricant will reduce friction and reduce or prevent metal-to-metal contact of the rolling elements with their raceways.
There are two basic types of bearing lubricants readily available: Oil and Grease.
Oil is free-flowing liquid, while grease has oil that is entrained in a thickened base.
Two Lubricants Advantages and Disadvantages:
The major advantages and disadvantages of oil and grease lubricants are as below:
Lubricant | Advantage | Disadvantage |
---|---|---|
Oil | Easy to distribute, lubes other components, less drag, easier to drain out and change. Better for high temperature. | May leak (environmental concern), then no more lubrication |
Grease | Remains in place, doesn’t leak out easily, improves sealing, and does not require monitoring. | Requires more labor to clean out and replenish. High temperature grease is very expensive. |
Oil Lubrication:
Rolling bearings are lubricated by oil lubrication, which can achieve good cooling and cooling effects, and is especially suitable for rolling bearings with relatively high operating temperatures.
The viscosity of the lubricating oil used in rolling bearings is about 0.12 to 0.2cm/s.
If the load of the rolling bearing is high and the working temperature is high, choose a high-viscosity lubricating oil. While a rolling bearing with a fast speed is suitable for a low-viscosity lubricating oil.
The disadvantage of using oil lubrication for rolling bearings is that oil lubrication requires the bearing to maintain a good sealing condition to avoid leakage of lubricating oil.
In addition, oil lubrication requires a more complicated oil supply device, which is not as convenient as lubricating grease in operation and increases the maintenance workload of bearings.
Oil Lubrication Guide:
Recommended General R&O Lubricant | |
Basic Oil | Refined solvent, high viscosity index mineral oil |
Additive | Rust inhibitors and antioxidants |
Viscosity Index | 80 min |
Pouring Point | -10℃ max. |
Viscosity Grade | ISO 32 to 220 |
Recommended Industrial Extreme Pressure Gear Oil | |
Basic Oil | Refined solvent, high viscosity index mineral oil |
Additive | Rust inhibitor and antioxidant, extreme pressure agent (EP) |
Viscosity Index | 80 min |
Pouring Point | -10℃ max. |
Viscosity Grade | ISO 100, 150, 220, 320, 460 |
Grease Lubrication:
When choosing a grease for an application, several of its properties need to be considered for the expected operating conditions.
The priority of these properties is as below,
1. Required oil viscosity at temperature of the bearing.
2. Grade for the operating temperature.
3. Soap base which is best for the application.
4. Availability of EP (Extreme Pressure) additives.
How Much Grease Should Fill ?
Once the available grease filling space for the bearing is determined, the amount of grease required will be calculated as a percentage of the available grease filling space.
The correct weight is important to ensure proper lubrication of all contact surfaces. Overlubrication is just as harmful as insufficient lubrication: for example, too much grease in high-speed bearings can cause overheating or higher starting and running torques.
Generally speaking, the amount of grease in the bearing should occupy approximately 25% to 35% of the available internal space.
In some very high-speed applications, the use of lubricants can be as low as 10% to 15%.
Commonly Used Grease Characteristics Table:
Manufacture | Ref | Grade | Base Oil | Thickener | Base oil viscosity | |
40℃ | 100℃ | |||||
kyodo Yushi | 1 | Multemp SRL | Polyol ester + diester | Lithium Hydroxystearate | 26 | 5.1 |
2 | Multemp SB-M | Synthetic hydrocarbon | Polyurea | 47.6 | 8.9 | |
3 | Raremax SUPER N | Mineral oil + synthetic hydrocarbon | Polyurea | 95.9 | 10.5 | |
4 | Multemp PS2 | Diester + synthetic hydrocarbon | Lithium soap | 15.3 | 4.7 | |
5 | Mutemp SRH | Polyol ester | Lithium soap | 83 | – | |
6 | Multemp SRM | Polyol ester | Lithium soap | 55 | – | |
7 | Multemp ET-K | Ether-based synthetic oil polyol ester | Aromatic diuretic | 95.1 | 12.3 | |
Kluber | 8 | BQH72-102 | Base oil, ester oil | Polyurea | 100 | 11 |
9 | BEP72-82 | Base oil, ester oil | Polyurea | 70 | 9.4 | |
10 | ASONIC GLY32 | Base oil, ester oil | Lithium-based | 25 | 5 | |
11 | ASONIC Q74-73 | Base oil, ester oil | Polyurea | 67.5 | 10 | |
12 | Isoflex LDS 18 special A | Ester oil, mineral oil | Lithium soap | 15 | 3.5 | |
13 | ISOFLEX TOPAS NB 52 | Synthetic ether + polyol ester | Compound barium soap base | 30 | 5.5 | |
14 | PETAMO GHY133 | Mineral oil + base oil | Polyurea | 150 | 18 | |
15 | BE 41-542 | Mineral oil | Lithium soap | 540 | 32 | |
16 | BE 31-502 | Mineral oil | Polyurea | 500 | 31 | |
Shell | 17 | AV2 | Mineral oil | Lithium-based | 130 | 12.2 |
18 | RLQ2 | Mineral oil | Lithium-based | 75 | 8.3 | |
19 | RL2 | Mineral oil | Lithium-based | 75 | 8 | |
20 | RL3 | Mineral oil | Lithium-based | 75 | 8 | |
Exxon Mobil | 21 | Polyrex EM | Mineral oil | Polyurea | 115 | 12.2 |
22 | Unirex N3 | Mineral oil | Lithium-based | 115 | – | |
23 | BEACON325 | Mineral oil | Lithium-based | 12 | 4 | |
24 | Unirex N2 | Mineral oil | Lithium-based | 115 | – | |
25 | Mobil grease 28 | Synthetic oil | Micro Adhesive | 29.3 | – | |
Cosmo | 26 | EMQ2(SBR) | Mineral oil | Lithium-based | 110.8 | 11.98 |
27 | PNG | Mineral oil | Lithium-based | 73.5 | 6.88 | |
Chevron | 28 | SRI 2 | (ISOSYN)mineral oil | Polyurea | 100 | 11 |
Lubcon | 29 | N2 | Ester | Polyurea | 150 | 22 |
Dupont | 30 | Krytox240 | (PFPE/PFPAE) | (PTFE) | 200 | 25 |
Jinzhi | 31 | Hangu 2 | Mineral oil | Lithium-based | 150 | 12 |