Spherical Roller Bearings Introduction
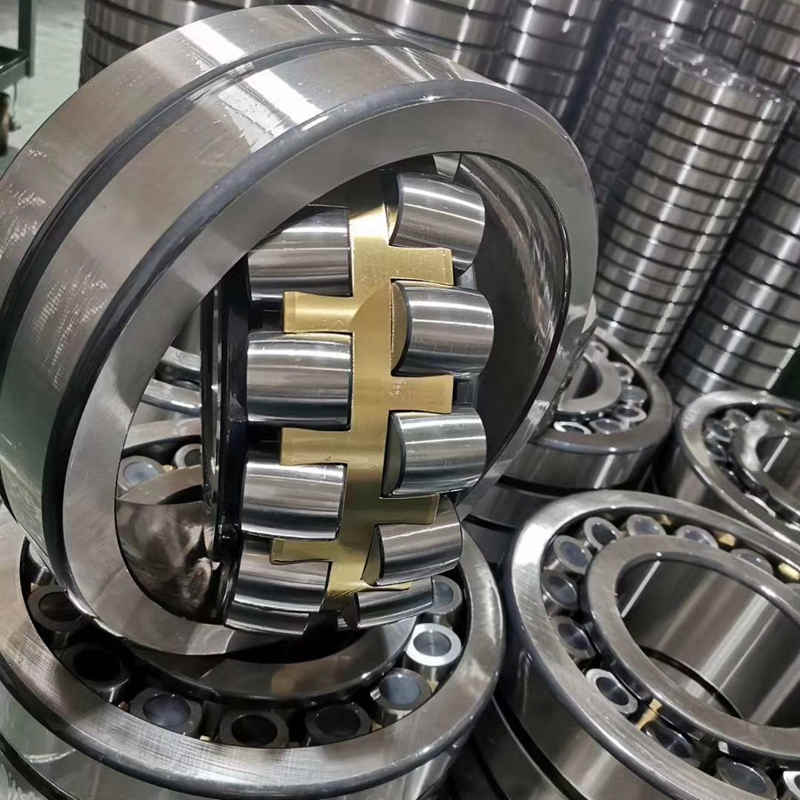
Spherical Roller Bearings Structure:
Spherical roller bearings have two rows of rollers, which mainly bear radial load, but also bear axial load in any direction.
With high radial load capacity, it is especially suitable for working under heavy load or vibration load. But it cannot bear pure axial load.
The outer ring raceway is spherical, so its alignment performance is good, and it can compensate for the coaxiality error.
Spherical roller bearings have cylindrical and conical bores.
The taper of the conical bore is 1:30 and 1:12.
This conical bore bearing has an adapter sleeve or a withdrawal sleeve.
The tapered inner hole self-aligning roller bearing can be easily and quickly assembled on the optical shaft or the stepper shaft.
Spherical Roller Bearings Main Applications:
Spherical roller bearings have wide applications.
For example, papermaking machinery, reduction gears, railway vehicle axles, rolling mill gearboxes, crushers, vibrating screens, printing machinery, woodworking machinery and so on.
Clearance:
For high-load and high-speed spherical roller bearings, when adjusting the clearance, the influence of temperature rise on the axial clearance must be taken into consideration.
Moreover, the reduction in clearance caused by the temperature rise must be estimated. That is to say, the axial clearance should be appropriately adjusted to be larger.
For low-speed and vibration-bearing bearings, clearance-free installation or pre-load installation should be adopted.
The purpose is to make rollers and raceway have good contact, the load is evenly distributed, and to prevent rollers and raceway from being damaged by vibration and impact.
Heating Methods:
1. Electric heating plate heating method
Put the bearing on the electric heating plate at a temperature of 100°C for a few minutes. This method is the most convenient.
For example, the bearing can be heated evenly by turning several times, and the efficiency is high. This heating method is suitable for both large and small spherical roller bearings.
2. Electric furnace heating method
The bearing is heated in a closed automatic temperature control electric furnace, heating is uniform, temperature control is accurate, and heating is fast.
It is suitable for heating many bearings in a batch.
3. Induction heating method
This mothod is especially suitable for the occasions where the inner ring is tightly fitted.
Because by using this mothod, only the inner ring is heated, while the outer ring is less heated. Therefore, bearings will be easily installed on shaft or the seat hole.
4. Electric bulb heating method
Using a 50W electric bulb to heat the spherical roller bearing, which can ensure heating temperature is about 100°C.
Small bearing can be placed directly on the bulb, and large bearing can be placed in the cone of the bulb.
The cover can prevent the heat loss of the bulb, and make the heating uniform. The cone cover can be adjusted up and down.
This heating method can be adapted to heating bearings of different sizes within a certain range.
5. Oil tank heating method
This is a widely used traditional heating method.
The oil groove is 50-70mm away from the bottom of the metal mesh. The bearing is placed on the net. Large bearing should be lifted with a hook.
Bearings should not be placed directly at the bottom of the groove, in order to prevent the temperature of contact part is too high or dirt deposited at the bottom of the groove enters bearing.